The workforce typically specialises in one or more pulping and papermaking operations, including wet end, dry end, pulping, stock preparation and handling, chemical recovery, electrical power generation, paper finishing and converting, steam generation, recovered fibre, and water services. Manufacturing of pulp, paper and paper products is critical for Australian households, offices, hospitals, food outlets and public buildings – from tissues and toilet paper, medical and sanitary products, to packaging and printing.
Key updates
Stable employment trends
Despite reports of lower recent demand from print publishing, most of the key occupations within the industry had relatively stable employment numbers, cumulative hours worked and individual hours worked in the Labour Force Survey.
Training providers not delivering VET qualifications
In their 2022 report, the Pulp and Paper Manufacturing Industry Reference Committee (IRC) noted that employers believe that there is a lack of Registered Training Organisations (RTOs) that can deliver the PPM Training Package, in a way that meets workforce needs. The IRC partly attributed this to the challenge of low financial viability for RTOs in maintaining such training programs, coupled with low turnover rate in the workforce, resulting in a limited number of potential new enrollees.
Opportunities
Downstream demand
Rising demand from packaging by online retailers and food producers has supported revenue over recent years, which is expected to continue.
Sustainability awareness and training
Industry operators have been investing in innovative practices, especially circular economy systems and manufacturing recycled and sustainable products. Designing promotional campaigns and training programs that showcase and deliver future-oriented skills, including in sustainability, circularity and design thinking and leadership, presents an opportunity to attract a skilled and motivated workforce.
Challenges
Underrepresentation of women
The 2021 Census showed women only accounted for 23% of this workforce, a 1% decline from 2016. Attracting priority cohorts may help with managing turnover in the context of an ageing workforce (45% are over the age of 50).
Digital and automation practices
The industry continues to invest in automation, which is reducing the number of employees required. However, industry revenues are declining at a faster rate than automation-related cost savings, which is adding to the pressure on employers to reduce staff costs.
Addressing imbalances in VET demand and supply
Training providers currently cannot sufficiently meet the specific needs of the industry, which means workers do not gain formal qualifications to complement their workplace-based learning and experiences, or to facilitate career mobility across occupations and industries.
Data monitoring priorities
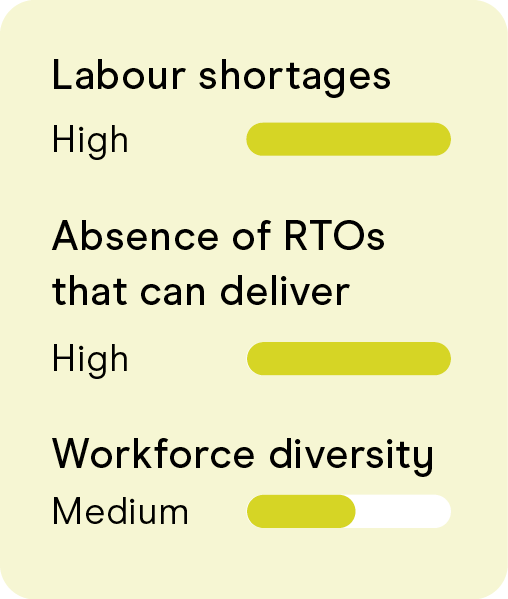
13,449
workers
(2021 Census)
1%
First Nations
(2021 Census)
2,200
2028 Projection
(JSA Projections)

23%
Female
(2021 Census)
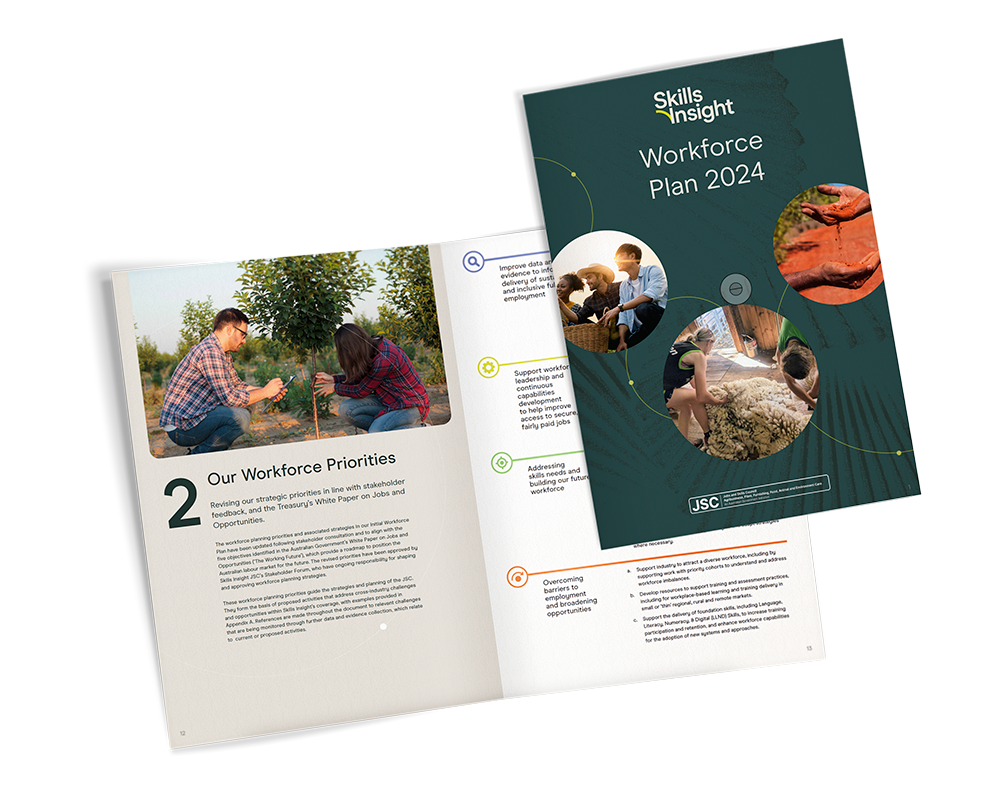
Workforce Plan 2024
The Workforce Plan describes workforce challenges and skill opportunities identified by stakeholders across the industries we work with and outlines strategies to address them.
The 2024 Workforce Plan outlines four key Workforce Planning Priorities to guide the strategies and planning of our JSC work, retaining the strategic intent of the Initial Workforce Plan, with modifications to align with the Australia Government’s White Paper on Jobs and Opportunities.